Centrifugal pumps are a fundamental category of vane equipment used extensively for the transportation of liquids in various industries. These pumps rely on centrifugal forces generated by the rotation of the impeller blades to move liquid. The fundamental design of centrifugal pumps is relatively straightforward, but they are highly effective and versatile, suitable for various applications. This article explores the design, operation, materials, advantages, and limitations of centrifugal pumps in detail. Companies like Ghaima Group of Companies provide expert solutions and services for selecting and maintaining these pumps, ensuring efficiency across different industries.
Introduction to Centrifugal Pumps
A centrifugal pump functions by converting rotational energy from a motor into kinetic energy in a liquid. This energy transformation occurs as the liquid passes through an impeller, which spins at high speed, creating a flow of liquid from one location to another. Traditionally, centrifugal pumps are constructed from materials like cast iron or stainless steel. In recent years, however, the range of materials has expanded to include options like aluminum and various thermoplastics, especially in applications where chemical resistance is a priority.
The choice of materials in centrifugal pump construction impacts the pump’s durability and efficiency. Stainless steel and other corrosion-resistant metals are highly favored for their longevity, especially in environments where the pump must withstand the effects of aggressive chemicals or high pressure.
Key Components of Centrifugal Pumps
Although there are many types of centrifugal pumps, they generally share a simple and efficient design. A basic centrifugal pump consists of three main components:
This is the heart of the pump. The impeller is responsible for generating rotational energy, which increases the velocity of the liquid. The impeller has a central hub, also known as the eye, from which the blades radiate outward. As the impeller rotates, the blades impart kinetic energy to the liquid.
Casing
The casing surrounds the impeller and directs the flow of liquid. It also helps to convert the velocity of the liquid into pressure, guiding the flow through the pump efficiently.
Pump Unit (Mechanical Unit):
The pump unit houses the impeller and includes the drive mechanism. Most centrifugal pumps are powered by an electric motor connected to a rotating drive shaft, but there are variations powered by hydraulic or pneumatic systems.
Types of Impellers
Impellers come in a variety of designs to accommodate different applications and flow requirements. The impeller design affects the pump’s performance, particularly in terms of flow rate, pressure, and efficiency.
- Open Impellers: These have blades attached to a hub with no sidewalls. They are suitable for liquids with solid particles but may have lower efficiency.
- Semi-Open Impellers: These impellers have a single sidewall and are commonly used in applications where moderate efficiency and solid-handling capacity are required.
- Closed Impellers: These are the most efficient impeller type, with blades enclosed by sidewalls. They are suitable for clean liquids or applications with higher pressure requirements.
Working Principle of Centrifugal Pumps
The operational process of a centrifugal pump is based on a simple yet effective mechanism:
- Rotation and Energy Transfer
When the motor drives the shaft, the impeller spins, causing the liquid at the impeller’s eye to accelerate outward along the blades. The centrifugal force generated by this rotation imparts kinetic energy to the liquid. - Fluid Movement and Pressure Increase
As the liquid exits the impeller, it moves through the casing where the velocity decreases slightly, but pressure increases. This pressure enables the liquid to overcome resistance as it flows through the pump discharge. - Discharge and Drainage
The design of the impeller and casing ensures that the liquid exits through the pump’s outlet at optimal speed and pressure. In many designs, the impeller is positioned so that the largest diameter aligns with the outlet, maximizing the pressure of the fluid leaving the pump. - Efficiency Optimization
To prevent backflow and to maintain pressure, the design of the casing directs the liquid toward the outlet, reducing energy loss and enhancing the pump’s overall efficiency.
Materials Used in Centrifugal Pump Construction
As centrifugal pumps have become widely used, the materials chosen for their construction have diversified. The choice of material depends on the specific application and the type of liquid being pumped.
Cast Iron: Common in general-purpose pumps, cast iron is durable and affordable but less resistant to corrosive chemicals.
Stainless Steel: Highly corrosion-resistant, stainless steel is ideal for applications involving aggressive chemicals and high pressures.
Aluminum: Lightweight and resistant to corrosion, aluminum is suitable for portable applications but may not be ideal for highly corrosive or high-pressure environments.
Thermoplastics: Used mainly for seals and gaskets, thermoplastics like Teflon and PVC are resistant to chemical degradation, ensuring longevity even in highly corrosive conditions.
Advantages of Centrifugal Pumps
Centrifugal pumps are favored for various reasons:
High Power and Efficiency
Centrifugal pumps are capable of delivering significant power, especially in industrial models where they achieve high flow rates and pressures. The minimum efficiency for standard centrifugal pumps typically exceeds 50%, with advanced models reaching efficiencies over 93%.
Versatile Application
These pumps can handle a range of liquids, from clean water to contaminated mixtures with particles. Modern designs reduce the risk of clogging, making them reliable for thick liquids or slurries.
Smooth Flow Output
The consistent rotational speed of centrifugal pumps allows them to provide a steady, non-pulsing flow, which is essential in applications that require precise flow control.
Limitations of Centrifugal Pumps
Despite their numerous advantages, centrifugal pumps also have limitations:
Air Sensitivity
Centrifugal pumps can experience issues if air enters the system, potentially causing cavitation, which can damage the impeller and reduce efficiency.
Pressure Limitations
Single-stage centrifugal pumps produce low pressure, making them less suitable for high-pressure applications. Multi-stage pumps can address this but often at the expense of efficiency.
Maintenance Requirements
Regular maintenance is essential to ensure the pump’s efficiency and longevity. Periodic inspection and cleaning of components are required, especially in harsh environments.
Applications of Centrifugal Pumps
Centrifugal pumps are widely used across industries due to their versatility:
Water Treatment and Distribution: Essential in water treatment plants, centrifugal pumps are used to distribute water through municipal pipelines.
Agriculture: Centrifugal pumps are used for irrigation and water supply in agricultural operations.
Oil and Gas: The oil and gas sector employs centrifugal pumps to handle fluids, including crude oil and refined petroleum products.
Chemical and Manufacturing: Corrosion-resistant centrifugal pumps are used to transport various chemicals and process fluids.
Maintenance and Care for Optimal Performance
To ensure uninterrupted operation, it is crucial to conduct regular maintenance of centrifugal pumps. Scheduled checks allow for the early identification of wear and tear on impellers, seals, and bearings. For expert maintenance, partnering with a professional electromechanical engineering company, like the Ghaima Group in Dubai, UAE, can help with the upkeep of these pumps and ensure long-term efficiency.
Conclusion
Centrifugal pumps remain a vital asset in many industries, from water supply to complex chemical processing. With a straightforward design and robust performance characteristics, these pumps offer high efficiency and power. By selecting appropriate materials and ensuring regular maintenance, centrifugal pumps can operate effectively over extended periods, providing reliable, cost-effective liquid transfer solutions. Whether in large-scale industrial operations or small-scale agricultural applications, centrifugal pumps continue to be indispensable tools in fluid management.
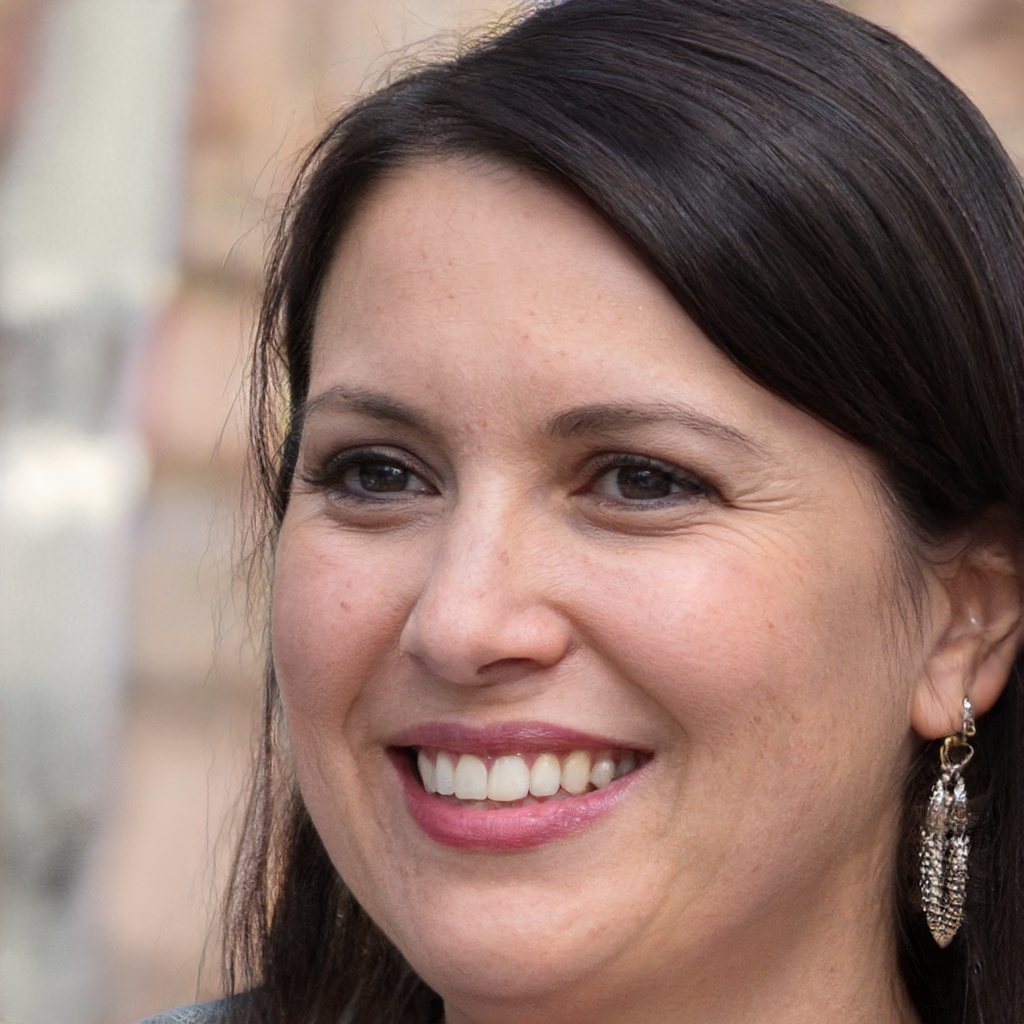
I am an Administrative Assistant with eight years of experience working alongside the executive team of a Fortune 500 company.